Keysight Technologies use simulation-powered digital twin to increase ROI on capital expenditures
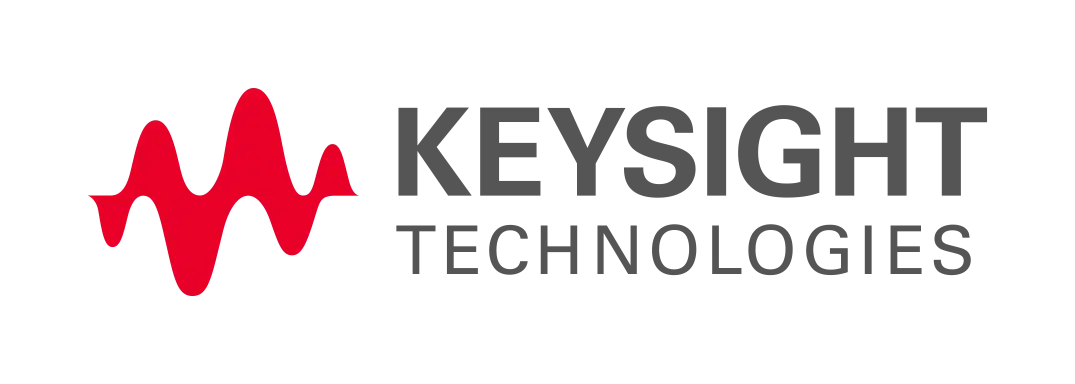
- Industry
- Electronics manufacturing
- Location
- Santa Rosa, California, United States
- Goal
- Streamline the wafer fabrication procedures using simulation-powered digital twins
Achievements with Simul8
-
-
Increased ROI on capital expenditures
-
-
Streamlined priority structure across the production line
-
-
Improved supplier agreements
The Challenge
The global chip shortage has accelerated the need for improved productivity on wafer production lines. For Keysight Technologies, a manufacturer of electronics test and measurement equipment and software, this presented an opportunity to meet increasing demands by enhancing its wafer fabrication procedures.
Its team of engineers turned to simulation to help them achieve process excellence, with a longer-term vision to build an operational simulation-powered digital twin fed by real-time data and living alongside the fabrication facility (or fab for short) for ongoing optimization.
The first phase of the project focused on wafer fabrication specifically, with phase two scheduled to include affiliated production lines with processes that are connected to wafer fabrication. The end result – a simulation-powered digital twin designed for ongoing optimization across the full production, from end-to-end.
“Stakeholders are beginning to understand the power of this simulation model and are requesting case studies to help them understand the impact of proposed changes on throughput and costs. The simulation has also helped operations managers understand the impact of changing job priorities or number of job-starts on throughput and completion dates.”
Process Engineer, Keysight Technologies
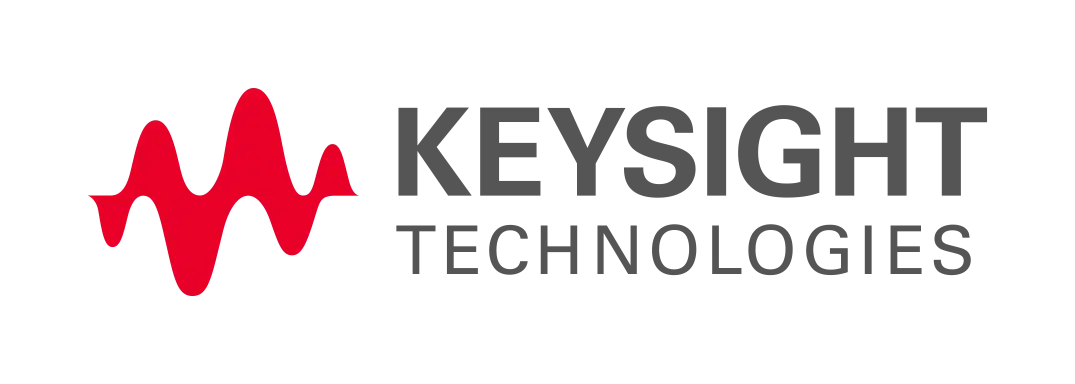
How did they do it?
Keysight wanted to identify and remove any barriers or bottlenecks that affected productivity within its fabrication facility to meet its long-term objectives for continued growth.
Its team of engineers had some ideas as to what might be obstructing throughput, including the volume of equipment redundancy, job prioritization, and the number of operators on site, but they were not so eager to commit to any structural changes to the fab layout without first testing them in a digital environment.
Using Simul8, the team highlighted potential throughput increases for specific tools across the factory floor. The model enabled them to continuously review processes within the fab layout and implement changes to increase the rate of throughput.
The Complexities of the Project
Wafer fabrication involves a series of up to 700 different processes to transform sand into a semiconductor slice that can be prepared for microchips and photovoltaics. This intricate work involves a combination of manpower and technical machinery.
Each segmented process on the production line is interdependent, and it is essential that the finished semiconductor is free from damage and imperfections.
However, the scale of the operation means there are risks of disruption throughout production. This could be in the form of machine downtime, operator availability, and work in process (WIP) volume i.e. the number of unfinished commodities in the inventory. Any shift in the status quo has the potential to impact Keysight’s productivity levels.
“If any machinery is to break down, this can severely hold up operations and increase our costs. By leveraging Simul8, we gained an excellent view of potential bottlenecks on the production line so that we could make the necessary tweaks ahead of time and avoid disruption.”
Operations Engineer, Keysight Technologies
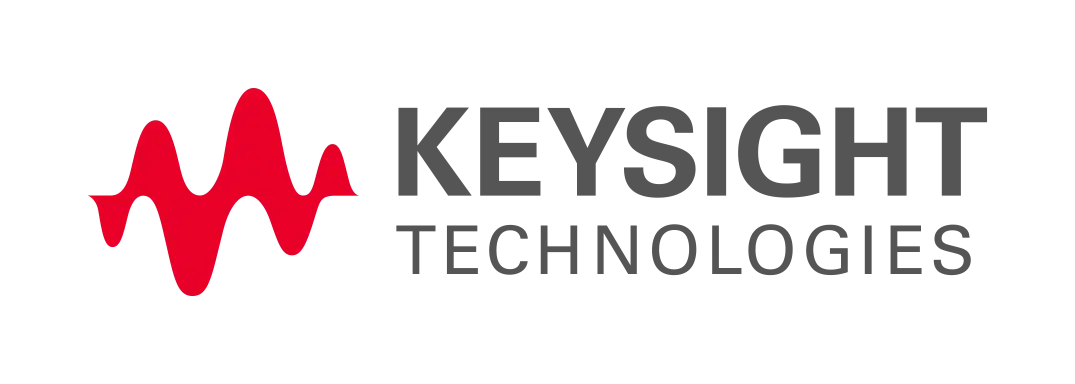
The Method
A specialist simulation team at Keysight worked with Simul8 to create a fully functioning simulation for Keysight’s wafer fabrication. The simulation was reviewed and improved over three iterations to enhance it with further features, including customized chamber modeling, dual assigned tools to capture redundant systems, and streamlined modeling features to allow results at shorter intervals.
The first iteration looked at the fabrication management policies. This included gauging the correct number of operators on the factory floor and identifying how the production line could handle any increase or decrease in WIP. Next, there was an in-depth look at each individual piece of machinery’s processes before moving onto reviewing assembly and exploring tool utilization and productivity impact.
Using Simul8, the team highlighted potential throughput increases for specific tools across the factory floor. The model enabled them to continuously review processes within the fab layout and implement changes to increase the rate of throughput. One process that was identified as having a bottleneck was photolithography, which involves etching a pattern of an electric circuit on the wafer’s surface, courtesy of a lithography tool.
Unfortunately, Keysight was experiencing issues with the uptime of the lithography tool and the supplier’s response times to maintenance requests, as it would take three days to get a response and seven before an engineer arrived on site to carry out repairs. Times that were unacceptable for Keysight’s needs. Using simulation, they were able to renegotiate maintenance agreements with this supplier to reduce downtime.
The Results
The wafer fabrication simulation has enabled Keysight to better understand the impact of priorities, lot size, and quantity of WIP on the floor. It has helped them determine the best structure to fit production needs, identify critical failure points, and examine the return on investment for key capital expenditures. It is also used to review staffing requirements and identify any gaps in coverage.
The simulation will help the team to review:
- Number of operators required
- Tool redundancy
- Critical KPIs review such as turnaround time and throughput
- WIP impact
- Lot size impact
“The simulation has provided a unique look at the priority structure of our fabrication facility, helping to drive decisions around the ideal structure to meet critical KPIs”
Operations Engineer, Keysight Technologies
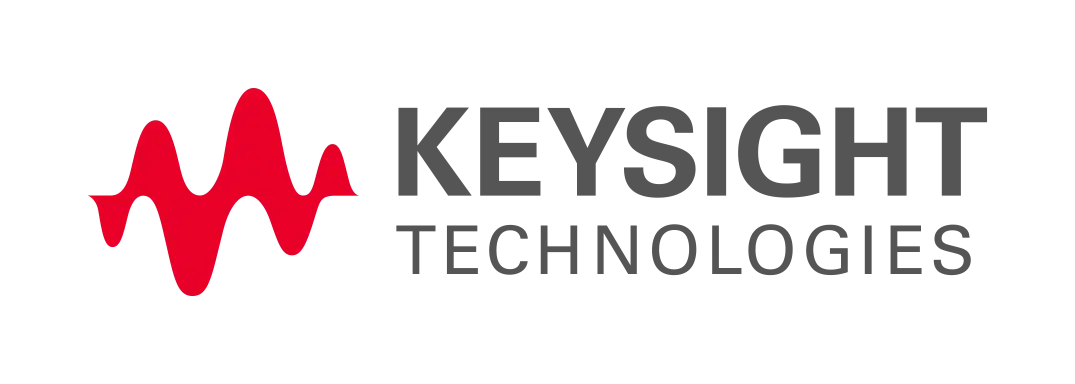
What's next for Keysight Technologies?
While simulation is commonly used for both process development and improvement across Keysight production and logistics, this project represents the most complex use-case yet, and also the biggest potential ROI.
The next phase is to continue to expand the simulation to other production areas connected to the wafer manufacturing line in order to optimize processes from end-to-end. Being fed with a supply of real-time data, this will enable the project to evolve into a simulation-powered digital twin that sits alongside the physical factory and can accurately forecast outcomes and facilitate recommendations on corrective actions required.
They will use the simulation-powered digital twin to simulate current states and then look ahead at the next few weeks to help identify any constraints or bottlenecks in the production line. To reach this point, the team is working on formatting all the required data. Having successfully presented the original simulation at company auditoriums, the Keysight simulation team will now be tasked with presenting digital twin adoption at boardroom level to encourage best practices that can be implemented across the whole business.
There are also plans to introduce a Simulation Center of Excellence within the company, demonstrating how integral the technology is for driving operational efficiency and process excellence.
Get a personalized Simul8 demo
Find out how Simul8 delivers serious impact, fast - arrange a live demo.
Learn more