Reduce waste and drive efficiency with Simul8
Rapidly test process improvements and identify the most effective strategies for reducing waste by combining simulation with Lean principles.
Why is simulation software a key tool for Lean projects?
Implementing changes without clear insights can result in costly mistakes, stakeholder resistance, and delays. Simul8 simulation software offers a powerful method to test, refine, and validate Lean initiatives before implementing real-world changes.
Leverage employee knowledge
Your employees are the best source of insights when it comes to improving processes. With simulation, you can integrate their knowledge, validate ideas, and show the tangible impact of proposed changes. By involving employees early, you enhance engagement, increase ownership, and strengthen stakeholder buy-in, making Lean initiatives more likely to succeed.
Risk-free experimentation
One of the biggest challenges of process improvement is the uncertainty of change. Simulation allows you to test multiple scenarios in a controlled, virtual environment—without disrupting operations. By modeling various "what-if" scenarios, you can identify risks, measure outcomes, and fine-tune strategies before any real-world implementation, ensuring confident decision-making.
Accelerate project timelines
Lean projects often require rapid iteration and quick adjustments. Simulation speeds up this process by providing immediate, data-driven insights into how changes will impact performance. Instead of relying on lengthy trial-and-error approaches, you can quickly evaluate different strategies, optimize workflows, and move forward with certainty—reducing project completion time significantly.
Why use Simul8 for implementing Lean?
Simulation software provides the ability to quickly experiment with different process improvement options, pinpointing the approaches that will most effectively reduce waste and add value to the customer.
Introducing a Lean approach can have an immediate impact on efficiency, productivity and profit.
Get implementation right first time
Implementing Lean manufacturing principles requires careful planning to ensure efficiency gains and cost reductions. However, making changes without a clear understanding of their impact can lead to unexpected bottlenecks, wasted resources, and unnecessary risks.
With Simul8, you can accurately visualize how a process will perform before and after implementing Lean improvements. By testing different scenarios in a risk-free simulation environment, you can confidently choose the best approach—ensuring that your Lean implementation is right the first time.
Instead of relying on guesswork or trial and error, simulation empowers you with data-driven decision-making, reducing waste, optimizing efficiency, and delivering immediate impact.Visual and interactive
Simul8 provides a visual, interactive and easy to understand representation of your process.
From long queues forming to workstations reaching capacity or bottlenecks slowing down output, simulation provides a dynamic way to showcase these challenges in real-time. Seeing a process in action - rather than reading reports or analyzing static charts - helps teams quickly grasp the issues and build consensus on solutions.
Assess return on investment
One of the biggest concerns when implementing Lean strategies is ensuring that the changes will be financially beneficial. Simulation allows you to take into account factors such as the expense of capital equipment, individual staffing rates or the return generated per work item.
By simulating different Lean scenarios, you can generate a detailed cost-benefit analysis, ensuring that every decision is backed by solid data.
Implement Lean manufacturing with simulation
Lean principles and simulation software together provide the ability to quickly experiment with different process improvement options to reduce waste and add value.
Read moreFind out how these organizations used Simul8 to transform decision-making
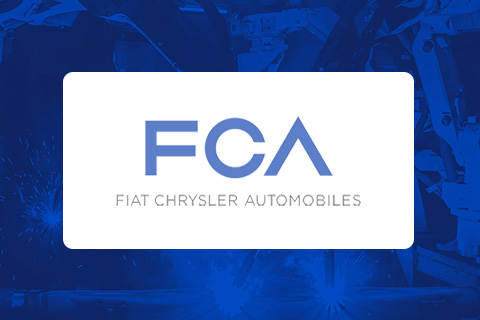
Meeting increased demand without additional costs
Fiat Chrysler improved manufacturing throughput by 39 units and increased revenue by $1,000,000 per day at its Brampton plant.
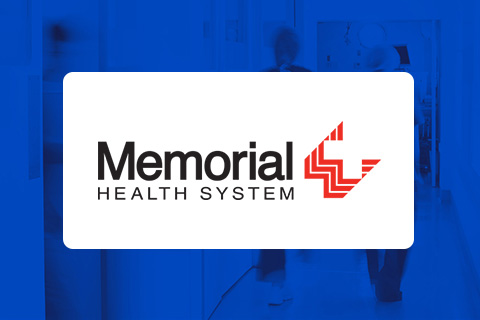
Ensuring the feasibility of investment and expansion
Memorial Health System improved patient waiting times and ensured the feasibility of a $31 million capital investment project.
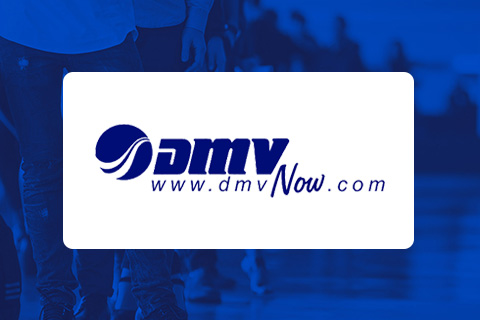
Optimizing staffing to reduce customer wait times
Virginia DMV identified a staffing model to reduce customer waiting times to 20 minutes or less across 74 customer service centres.
Six Sigma and Simulation
Read our whitepaper, Less is More, to learn how a highly experienced Six Sigma Black Belt approaches simulation projects.
Read now