FUJIFILM tests large-scale process changes to meet a 400% rise in demand
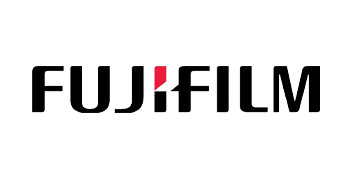
- Industry
- Manufacturing
- Location
- New Castle, U.S.
- Project goals
- Find an optimum production approach to meet a 400% increase in demand.
Achievements with Simul8
-
-
Evaluated a range of potential throughput improvements within just a few days
-
-
Analyzed return on investment of new machinery and staffing to increase output
-
-
Identified a production approach that would increase throughput to meet future demand
About the project
FUJIFILM Imaging Colorants (FFIC) is a global leader in developing and manufacturing high-performance inkjet inks, pigments and dyes.
With more than twenty-five years of recognized innovation, FFIC offers an unparalleled mix of R&D expertise and advanced manufacturing capabilities to support the needs of customers across a diverse range of sectors.
With continued technological developments driving the rapid expansion of inkjet printing technology into new applications areas, FFIC expects customer demand to increase fourfold over five years.
To meet this substantial rise in demand, FFIC utilized Simul8 to evaluate a range potential throughput improvements to its packaging operations within just a few days.
With Simul8, FFIC was able to investigate large-scale process and operational changes and accurately assess the short and long-term impact on KPIs – all within a risk-free, cost-effective environment.
"Simul8 gave us the ability to evaluate a wide berth of process improvement options, all with potentially large financial or engineering implications, without spending any significant money or time to investigate."
Project Manager, FUJIFILM Imaging Colorants
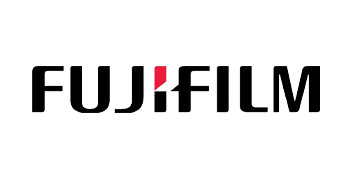
Simulating the packaging line process with Simul8
Driven by a forecasted fourfold increase in small packaging demand, FFIC turned to simulation to explore changes to meet or exceed production, as well as providing flexibility to vary throughput as needed.
In FFIC’s current packaging setup, bulk material is fed into a clean-room environment where filling takes place one container at a time. Due to the clean-room requirements, this process requires at least one operator at all times.
Once the containers are filled, they are then passed down a conveyor outside of the clean-room, through a boxing station, onto palletizing and finally warehousing, where non-clean-room activities are performed by a second operator.
The line operates on a five day by eight hour shift schedule, where filling equipment is cleaned at the start and end of each shift, as well as during the arrival of new bulk material.
Building the baseline simulation
Using Simul8 for the first time, FFIC’s Project Manager, Eric Kurtz, was quickly able to simulate this entire packing line process and resource.
Existing plant metrics were utilized to confirm the accuracy of the baseline simulation model, allowing the impact of improvement scenario simulations to be properly assessed.
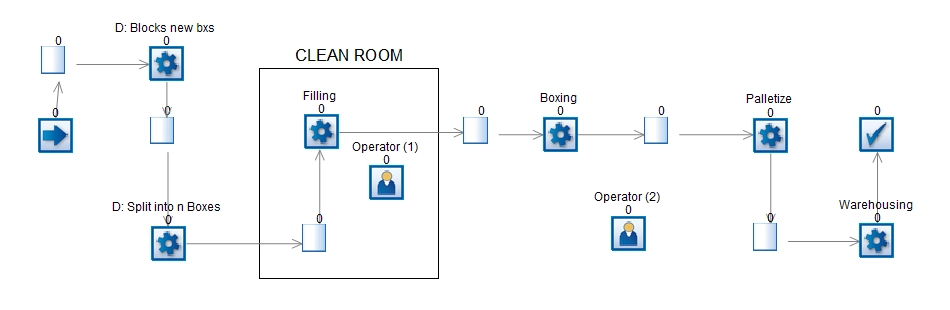
Measuring the success of improvement scenarios
Through discussions with stakeholders involved in managing the packaging operation, FFIC decided on a set of key performance indicators to compare the effectiveness of potential improvement scenarios within Simul8:
- Operator Utilization (%)
- Operating Costs (Including operator and machine/utility costs)
- Capital Costs
- Throughput by number of individual containers
- Throughput by total volume in liters
- Total Asset Utilization (%)
- Three Year Net Present Value (NPV) (used to analyze the profitability of a projected investment)
To understand the long-term impact of improvement scenarios, FFIC also evaluated each against current and future product mix demand; ranging from a present demand of mainly 20L packages, to a longer-term product mix with a higher proportion of smaller 10L packages required in the next five years.
Before deciding on improvement scenarios to evaluate, some key issues were identified as contributing factors to the inability to meet projected future demand:
- Limited throughput
- Use of a semi-automated process
- Low asset and operator utilization
To overcome these bottlenecks, a range of process improvement ideas were suggested for evaluation using Simul8, including:
- Removal of the clean-room requirement (allowing one operator to move to other production activities)
- Installing new two or four multi-head filler equipment, providing a parallel 10L packaging line
- Reducing production setup and changeover times
- Modifying operator shift patterns
- Changing the number of available operators
"The insight provided through using simulation enabled us to make a strategic, long-term capital plan, as well as product offering decisions. The project has been quickly approved and the design and engineering work is already in process, with the goal of implementation later this year."
Project Manager, FUJIFILM Imaging Colorants
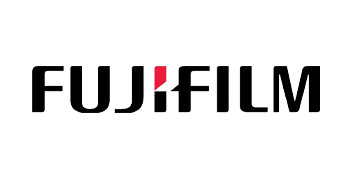
Identifying a flexible, scalable solution to meet long-term demand
Completing the project within a few days, FFIC’s Project Manager, Eric Kurtz utilized KPI and ROI results from Simul8 to compile a detailed report for stakeholders of recommendations on improvement options.
Several initial conclusions were highlighted from the simulations:
- Setup, clean-up, changeover reductions and shift pattern changes had minimal to no impact within any of the simulation scenarios.
- Throughput is influenced by activity availability and constrained by operator availability.
- Adding extra packing line operators would significantly increase the throughput.
- Net Present Value is directly tied to throughput, and actual demand.
From these findings and the results of the other simulation scenarios, it was recommended that FFIC scope and install a four-head semi-automated filling line.
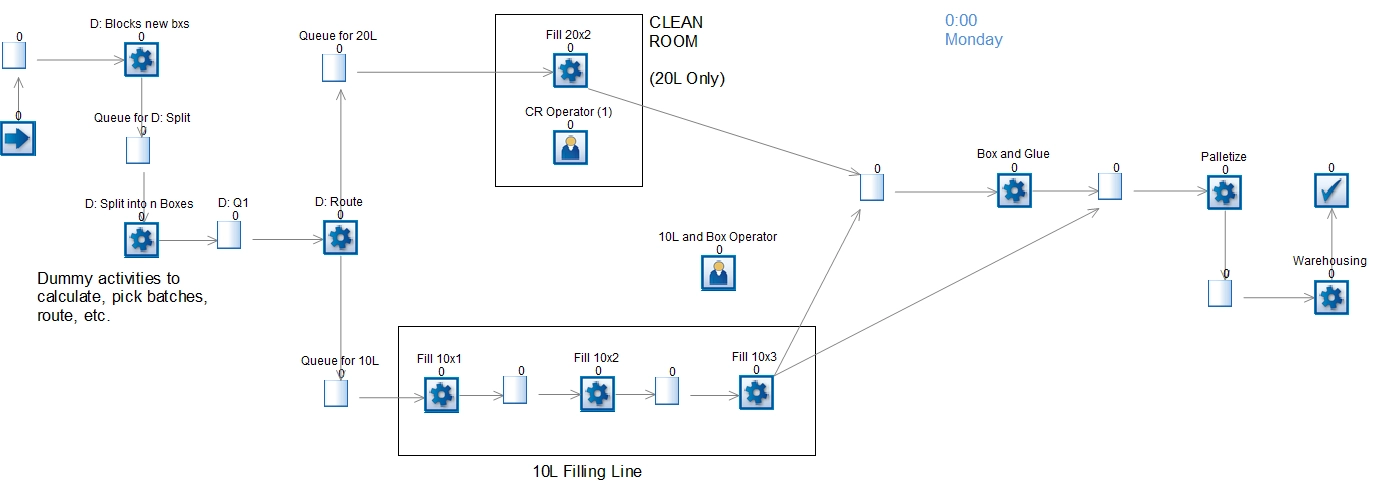
Why was this chosen as the recommended solution?
Although the four-head semi-automated filling line option requires the largest up-front capital cost, the small increase in capital over a two-head filler was found to provide an increase in overall capacity of more than 10 tonnes per month in comparison.
Combining this four-head filler option with three operators (one for clean-room activities and two for the rest of the line), was also found to provide a potential 338% increase in throughput and a 29% increase in total asset utilization in five years.
This option also provides FFIC with flexibility to increase overall system throughput over time. As it will take some time to reach projected demand, the four-head filler can initially operate as a two-head, and then be expanded to four-heads when needed.
As a result of the insight provided by the project, FFIC have now been able to develop a strategic, long-term capital plan to begin implementation of the packing line project this year.
From the success of this project, FFIC are also planning several other process improvement projects across the organization using Simul8, spanning engineering, R&D, manufacturing operations, and general business improvement.
Learn more about Simul8 for manufacturing process improvement
Find out more about how simulation is used by manufacturing organizations, read more case studies and access a range of learning resources.
Learn more