Implementing Lean Manufacturing with Simulation
Lean manufacturing can have an immediate, positive impact on efficiency, productivity and profit.
Simulation software enables you to quickly experiment with Lean process improvement options and pinpoint ways to reduce waste and add value to the customer.
What is Lean manufacturing?
Lean manufacturing is a systematic method for the elimination of waste within a manufacturing process.
Waste, or Muda, is defined in the Toyota Production System (TPS) as anything that doesn’t increase value for your customers. When waste is removed, processes are streamlined, valuable time and costs are saved and customer satisfaction is improved.
Lean manufacturing is a management philosophy derived from Toyota and their way of working to remove waste and improve customer value. Waste can include factors that might not usually be usually be thought of as waste including as overproduction, high levels of inventory, items which need to be reworked, processing or waiting times and unnecessary movement.
Exactly what value means will be different depending on your process and customer but can involve looking at key performance indicators such as throughput, productivity, cost and amount of work in progress.
What are the common wastes of Lean manufacturing?
-
Defects
Defects are products or services that are out of specification. They need extra effort or resources to fix and lead to increased costs and lost time, either through repairs or having to start over.
-
Overproduction
Overproduction, where production exceeds customer demand, is considered the most harmful waste as it itself creates additional waste including excess inventory and transportation.
-
Waiting
Waiting occurs whenever items aren’t in transport or being processed. For example, employees wait for materials, equipment waits for maintenance, or work in process waits for the employee to return.
-
Not utilizing talent
By under-utilizing employee skills and knowledge, organizations limit their potential. Developing talent and engaging employees in process improvement can reduce waste.
-
Transportation
Transportation occurs whenever products are transported from one location to another. This can increase the risk of damages, additional waiting time and costs.
-
Inventory excess
Inventory, such as raw materials, work-in-progress or goods which are sitting idle, is considered waste as it hasn’t yet contributed value to the end customer.
-
Motion waste
Unnecessary motion can occur due to inefficient layouts or searching for mislaid items. It can also increase the risk of damage to equipment or cause employee injuries.
-
Excess processing
Excess processing is any activity that isn’t needed to produce a functioning product or service and can occur due to any unnecessary or drawn-out processes.
Examples of waste reduction techniques in manufacturing
The implementation of Lean manufacturing by making value flow at the pull of the customer (Just-In-Time) prevents and eliminates waste in your processes.
Changes to manufacturing processes that can be considered to reduce waste include:
- Leveling production to match demand
- Reducing end-to-end cycle time to less than customer's expectation of reasonable wait time
- Using Just-in-Time delivery schedules with suppliers
- Monitoring quality in a responsive manner
- Properly fixing all problems at the source and accepting the higher short term cost of doing this
- Reducing change over time so that batch sizes can be reduced cost effectively
- Empowering and training employees to participate in continuous improvement and increasing communication and visibility to make this easy for them
In order to completely eliminate waste, all of these process changes should be considered together – but with a wide range of parameters to consider (e.g. batch sizes, J-i-T schedules, acceptable cycles times, Kanban quantities, container sizes), making these changes without affecting other processes or adding other forms of waste can be difficult. This is why many manufacturers rely on simulation software when planning and implementing Lean projects.
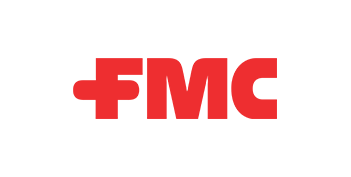
“Simul8 gave us a technical way of understanding capacity, identifying bottlenecks and changing data to achieve new capacities, new goals and new logics. We never had this ability before.”
Project Manager, GPS Lead and Planning Specialist, FMC Technologies
FMC Technologies increased manufacturing throughput by 50%, removed bottlenecks and forecasted 5 year production to meet demand using Simul8.
Read the case studyHow can simulation support Lean manufacturing techniques?
Simul8 discrete event simulation software can show accurately how a process will behave, both before and after implementing a Lean manufacturing approach. This means you can get Lean implementation right first-time.
Simulating processes gives manufacturers a real advantage. Being able to present a dynamic and animated display of processes is a very powerful way of highlighting constraints in a system and is very effective in building buy-in for both operational and managerial staff to recognize the need for change.
Whether your simulation is showing a large queue building-up, or a series of activities grinding to a halt due to a lack of stock, nothing is more effective at communicating these types of issues than letting stakeholders see this happening for themselves.
Discrete event simulation software enables the implementation and monitoring of Lean manufacturing processes, providing you with:
- An accurate prediction of likely cost savings of introducing Lean to manufacturing process
- A detailed understanding of exactly how the parameters impact overall performance
- The ability to test any number of combinations of parameter values and decide which are best for your implementation
- Accurate predictions of the speed of response your customers will see
- A quick and easy-to-run device for obtaining buy-in from senior management or training employees
- A tool for empowering employees by allowing their process improvement ideas to be tested with easy-to-understand visual and numerical feedback on its effectiveness