Vidant combines simulation and Six Sigma techniques to maintain left without treatment targets of under 2%
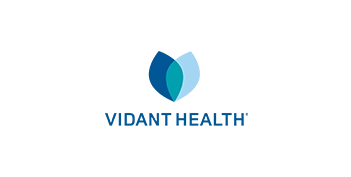
- Industry
- Healthcare
- Location
- Kenansville, North Carolina, U.S.
- Goals
- Test and support two Lean Six Sigma process improvement projects
Achievements with Simul8
-
-
Created pilot simulations and achieved results within a few hours
-
-
Determined how to maintain left without treatment rate of under 2% despite increasing demand
-
-
Assessed the feasibility of introducing a Pharmacy Technician to improve patient medication history collection
About the project
Vidant Duplin Hospital, part of the Vidant Health System, is a 101-bed, not-for-profit hospital located Kenansville, eastern North Carolina.
As a small, rural hospital, with limited income and resources available, Vidant Duplin utilizes Lean Six Sigma techniques to eliminate waste and maximize resources to improve quality of care, patient safety and experience.
With increasing demand for the hospital’s emergency department (ED) services, Process Improvement Coordinator’s Amanda Peterson and Raul Medina utilized simulation for the first time to test and support two Lean Six Sigma process improvement projects:
- Determining how to maintain a LWOT (left without treatment) rate of under 2% with growing ED patient volumes.
- Assessing the feasibility of implementing a Pharmacy Technician into the ED to improve the accuracy of collecting patient medication histories.
Using Simul8 simulation software, Amanda and Raul created simulations of these processes in less than four hours, successfully gaining valuable insight in a risk-free environment.
From these initial projects, Amanda notes that simulation has been well-received across the hospital, not only as an opportunity to validate team’s hard work, but as a complementary tool for Lean Six Sigma process improvement.
"I think that simulation provides a really unique opportunity to allow us to test ideas and experiments. The team may suggest adding another provider or more beds and simulation could allow us to see if it would work. From a Lean perspective, that is one of the things we really liked - there is a lot of opportunity."
"As Duplin is a lower income, low resource area patients and communities face challenges such as access to care or a limited number of primary care providers, we believe that simulation can help us to understand what resources are needed.
I think that simulation has been really advantageous for us as a small, rural hospital."
MS, RDN, LDN, Vidant Duplin Hospital
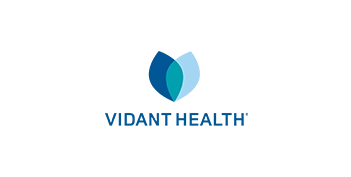
Understanding the impact of growing ED demand on LWOT rates
Patient visits to Vidant Duplin Hospital’s emergency department (ED) have been rising over the last few years, as more patients from surrounding counties utilize its services. As ED visits and acuity increase, there is also an additional risk of more patients leaving without treatment (LWOT).
To maintain a yearly LWOT rate of less than 2%, in line with national benchmarks, Vidant Duplin needed to assess whether the hospital’s ED could maintain this standard as patient visits grew.
Simul8 simulation software was utilized by Raul Medina, Lean Six Sigma Black Belt and Lead Process Improvement Coordinator, to understand the effect of increasing ED utilization on LWOT rates and assess potential solutions to reduce this impact.
Rapidly simulating emergency department processes
Despite not having used Simul8 or other simulation software before, Raul was able to build a simulation within just a few hours, modeling the entire patient ED process; from pre-registration, triage, the treatment of the patient, final registration and through to departure. The simulation also utilized existing ED data, including median times for total stay, to enhance the accuracy of the results.
As more patients arrived in the simulation, LWOT rates were displayed, as well as acuity levels - a measurement of the intensity of nursing care required by a patient, with one being the highest level and five being the lowest.
At current patient arrival rates, the ED were seeing 78 patients per day on average, with a LWOT rate of 1.7%. However, with ED patient volumes increasing by 10% each year for the last four years, the team knew the maximum 2% LWOT threshold rate would likely be crossed, unless department processes could be changed to accommodate this increase.
"The ED would adapt and change its processes on a daily basis sometimes, just based on the acuity of the patients or the number that they saw. They are very adaptable and able to change their processes, open different places up and do more triage or do things in a certain way."
Using the base simulation, Raul was able to quickly test a range of process changes to help the ED improve this flexibility using existing resources.
This included the introduction of an area for patients waiting on labs or radiology results to free up room for additional patients in the main ED.
The simulation showed that using this approach, even with an increased average workload of 89 patients per day, LWOT rates would still be maintained at 1.7%, without the need for additional resources.
"You can say, ‘What happens if I increase my person load coming to the ED by 20%?’.
You can plug that into Simul8 and ask what that would do to the resources and how many LWOTs there would be, or what the efficiency would be of staff and whether we would be burning them out."
Lean Six Sigma Black Belt and Lead Process Improvement Coordinator, Vidant Duplin Hospital
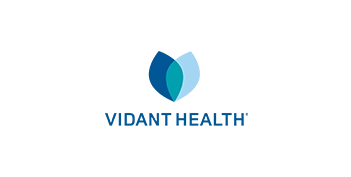
Implementing an ED Pharmacy Technician to improve the accuracy of medication histories
Inaccurate medication histories present a serious safety concern for patients and healthcare organizations. Previous studies suggest that a little less than half of medication histories collected contain errors (e.g. incorrect dosage, omissions, etc.), of which, almost a fifth have potential to cause the patient harm.
However, national best practices for collecting medication histories have yet to be determined.
Vidant Health System wanted to investigate an approach to standardizing practices for collecting medication histories across their system. However, with hospitals in the system ranging from small and rural facilities, to a large academic teaching centre, a solution would not be one size fits all. Vidant Health’s Lean department were tasked with considering potential local constraints.
Simul8 was utilized by Process Improvement Coordinator, Amanda Peterson, to test an approach to standardizing medication histories and collect data and observations to support recommendations to senior leadership.
The process and simulation results
Using Simul8, Amanda developed a simulation to assess the feasibility of integrating a Pharmacy Technician into Vidant Duplin Hospital’s ED to collect patient medication history - a process currently carried out by nurses.
The process also involved the use of scripted patient interviews for collecting comprehensive medication history. The interviews covered everything from prescription medication to over the counter medication, including dietary supplements and ointments. Each interview could take anywhere between 15 to 30 minutes, depending on the patient’s medical history and how accurate the records have been up to that point.
Amanda’s simulation mapped out this entire process, utilizing existing ED data along with the required resources. The Pharmacy Technician was added to the ED simulation for seven days a week, operating an eight hour shift during the busiest hours (3.00PM and 11.00PM).
“We kept the simulation fairly simple. Even with that simplicity, it still worked and it mirrored what we are seeing now. I was very surprised at how simple the model was to build. Overall, it only took me about 60 minutes to develop the simulation.”
Patients were prioritized so that the Pharmacy Technician would see them based on the order to consult. If the patient had to be admitted, then technician would know that that patient would come first.
As this process could take up to 30 minutes, other constraints and expiry times were also modeled, so when the Pharmacy Technician was busy collecting histories, then this would default to an emergency department relief nurse.
The simulation identified that the implementation of a Pharmacy Technician would result in 14 medication histories collected per day. This was an increase over the current 10 per day, even with a lengthier, comprehensive scripted interview process for collecting medication histories from patients.
Next steps for Vidant Duplin Hospital
"We were really pleased with our simulation. We got a lot out of it because this was a new process.
Our role was to share the findings with our hospital executives and senior leadership in the Lean Steering Group, which is a group of Lean practitioners all working together. We also shared this with the emergency department and pharmacy work groups in our system.
We plan to share the results with the community hospitals in our area both within and outside of our system, because rural hospitals face a lot of the same constraints.
We were using the results to support a proposal for which we were seeking grant funding, so the use of simulation helped to smooth this process and helped us to organize our thoughts for the proposal, especially because we did not have the baseline data."
Webinar
Discover how simulation was used to evaluate ‘step-down’ beds, improve patient throughput, quality of care and patient safety.
Watch webinarHealthcare Resources
Explore our healthcare resources to learn how Simul8 can benefit your organization.
Learn moreLearn more about Simul8 for healthcare process improvement
Find out more about how simulation is used by healthcare organizations, read more case studies and access a range of learning resources.
Learn more