FMC Technologies increases production output by 50%
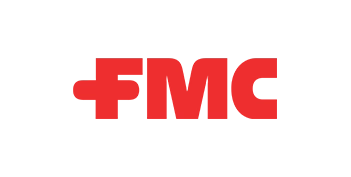
- Industry
- Manufacturing
- Location
- Houston, Texas, U.S.
- Project goals
- Increase output to meet growing demand
Achievements with Simul8
-
-
Increased manufacturing throughput by up to 50%
-
-
Increased output of Christmas trees by over 100%, with no additional spend
-
-
Saved millions of dollars by ensuring on-time delivery of products to clients
-
-
Increased monthly capacity of SCMs by 50% with no capital expenditure
About the project
Named by Forbes® Magazine as one of the World’s Most Innovative Companies, FMC Technologies has over 20,000 employees and operates 28 production facilities in 17 countries. The organization designs and manufactures products, and provides services for the oil and gas sector that include:
- Subsea systems
- Fluid control
- Measurement solutions
- Material handling systems
Simulation was first introduced to FMC Technologies by GPS Lead and Planning Specialist Ricardo Fernandes when he began working at the plant. Ricardo used Simul8 at university and saw a huge opportunity to use simulation to improve manufacturing processes.
Leading a small team, Ricardo has delivered a variety of simulation projects, from increasing the capacity of SCMs by 50% (the control center of Christmas trees), to identifying bottlenecks in manufacturing lines and forecasting 5 year production to ensure output is aligned with market growth.
"If we hadn't used Simul8 and were unable to measure capacity; that would mean not being able to deliver on time and therefore be an erosion of profit."
Project Manager, GPS Lead and Planning Specialist, FMC Technologies
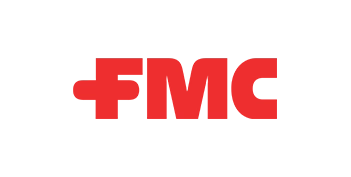
Meeting the challenge of maximizing output to meet increased demand
A sharp rise in market demand meant FMC Technologies’ operations had to shift from producing small quantities of equipment, to delivering bigger quantities for much larger fields. The increased pressure on production meant they needed a tool that could understand current production and test improvement scenarios to eliminate bottlenecks and maximize manufacturing capacity.
Simul8 was the optimum solution: enabling FMC Technologies to test multiple product combinations moving through a line to determine the most efficient process. Using simulation software, these product combinations could be tested risk-free, without impacting manufacturing production.
With financial penalties incurred upon late delivery to clients, FMC Technologies also needed to be able to validate their ability to deliver to agreed timescales.
Through the use of Simul8, not only could FMC Technologies prove their ability to deliver on time, they could also plan how this would be achieved and communicate these strategies to senior decision makers. This provided the evidence for capital expenditure and confidence in proposals.
FMC Technologies used Simul8 simulation software to:
- Understand and optimize processes
- Understand resource requirements
- Increase production
- Reduce risk
- Identify bottlenecks
- Inform spending decisions on staffing and equipment
"Simul8 gave us a technical way of understanding capacity, identifying bottlenecks and changing data to achieve new capacities, new goals and new logics. We never had this ability before."
Project Manager, GPS Lead and Planning Specialist, FMC Technologies
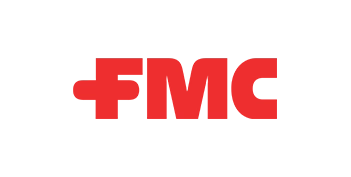
How has simulation helped remove bottlenecks and increase manufacturing output?
FMC Technologies use Simul8 to continuously test, evaluate, and implement manufacturing improvements based on results. Below are some of the many ways Simul8 is being used across the organization:
Identified bottlenecks
FMC Technologies has used Simul8 to identify bottlenecks and ensure that these are removed without introducing them elsewhere. In a recent simulation project, a bottleneck at the testing stations was indentified and line layout was revised to introduce a fork design with double the number of test stations.
Increased production
Simulation has been used to understand viable methods of increasing production by testing the impact of reducing cycle times and the addition of new machinery. Simul8 identified that reducing cycle times would have the greatest impact, as well as how much cycle time needed to be reduced by, and at which stations, in order to increase productivity.
Forecasted demand
Simul8 has been used to forecast five year production, ensuring FMC Technologies' ability to deliver against their clients’ required output, as well as in accordance with future market demand. This has also enabled the company to advise clients where there will be a need for future investment in new machinery.
Line balancing
With multiple products entering a single line and millions of possible combinations, Simul8 was used to understand the product input mix and balance the line. Simul8 also helped to identify constraints across existing physical assets including people, cranes and pits. By re-balancing the line and addressing constraints, output increased by up to 50%.
Isolated single product in multi-product line
Simul8 enabled FMC Technologies to understand the performance of one product in a multi-product line, if given 100% dedicated resource. This was achieved through a simulation that mirrored the physical line layout with only one product assembly. Simulation was the only tool that could rapidly calculate exact throughput without halting production.
Simulation results increased throughput for FMC Technologies
Simul8 has enabled FMC Technologies to increase throughput across the organization by an average of 15 - 20%. This has been as high as 50% in the case of the SCM Assembly – the main component and control center of the Christmas tree.
Since FMC Technologies began using Simul8, Ricardo and his team have transformed manufacturing processes across the organization. By understanding capacity and effective line balancing of their multiple-product line, they have successfully increased output to meet rising market demand. This has been achieved through testing multiple product input combinations and eliminating the formation of bottlenecks.
Using Simul8, FMC Technologies has saved millions of dollars by ensuring on-time delivery of products to clients. Cost savings have also been made by avoiding spend on expensive manufacturing equipment and resources. In many cases more effective solutions have been found elsewhere, such as in changing the layout of the line, rather than on capital expenditure.
This is where simulation has proven to be most effective, enabling multiple scenarios to be tested virtually and solutions to be identified without compromising production or losses in revenue.
With the ability to develop rapid simulations and optimize processes based on the results, FMC Technologies continues to use simulation as an integral operational planning tool to streamline their manufacturing processes. Using Simul8, FMC Technologies is able to maintain a competitive advantage and ensure they are able to meet growing market demand.
Learn more about Simul8 for manufacturing process improvement
Find out more about how simulation is used by manufacturing organizations, read more case studies and access a range of learning resources.
Learn more