Eliminate defects, slash costs and increase profitabilily
The powerful combination of Simul8 and Six Sigma enables process improvers to make confident and informed decisions.
What is Six Sigma?
Six Sigma is a disciplined, data-driven approach and methodology for eliminating defects in any process – from manufacturing to transactional and from product to service.
Six Sigma seeks to improve the quality of the output of a process by minimizing variability in manufacturing and business processes. It uses a set of quality management methods, mainly empirical, statistical methods, and creates a special infrastructure of people within the organization who are experts in these methods e.g. Six Sigma Black Belt.
Each Six Sigma project an organization undertakes will follow a defined sequence of steps and has specific value targets, for example to reduce cycle time, decrease costs, improve customer satisfaction, and increase profit.
Six Sigma is divided into two methodologies, DMAIC and DFSS:
- DMAIC (Define, Measure, Analyze, Improve, Control) focuses on improving existing processes and performance
- Design for Six Sigma (DFSS) focuses on generating new processes, products, and services to meet customer needs (CTQ) at the Six Sigma level
How can simulation support Six Sigma projects?
Simulation enables realistic representations of systems to be easily created and tested in a risk-free environment to ensure improvement ideas will eliminate defects, reduce costs and increase profitability.
Power and precision of simulation
Discrete Event Simulation (DES) offers a more powerful study and insightful results than static analysis or a mathematical equation.
The statistical rigor available through valid, verifiable simulation makes it an ideal fit with both DMAIC and DFSS methodologies.
Comprehensive analysis capability
Simulation allows users to compare defects, predict tolerances, and measure various indicators in a Six Sigma analysis process.
This includes financial, operational, and customer satisfaction indicators.
Dynamic simulation with core building blocks
Simul8 provides dynamic analysis capability and the basic entities and logic to create realistic simulations of any process or manufacturing facility.
These core building blocks, combined with attributes (Labels) and Logic (Visual Logic), enable the simulation of even the most complex systems.
Scenario planning and Results functionality
Turning static data into a dynamic simulation helps answer 'what-if' scenarios in the planning stage, ensuring the right process is implemented the first time.
Significant aspects of parts traversing through a facility can be captured using Simul8’s diverse results functionality.
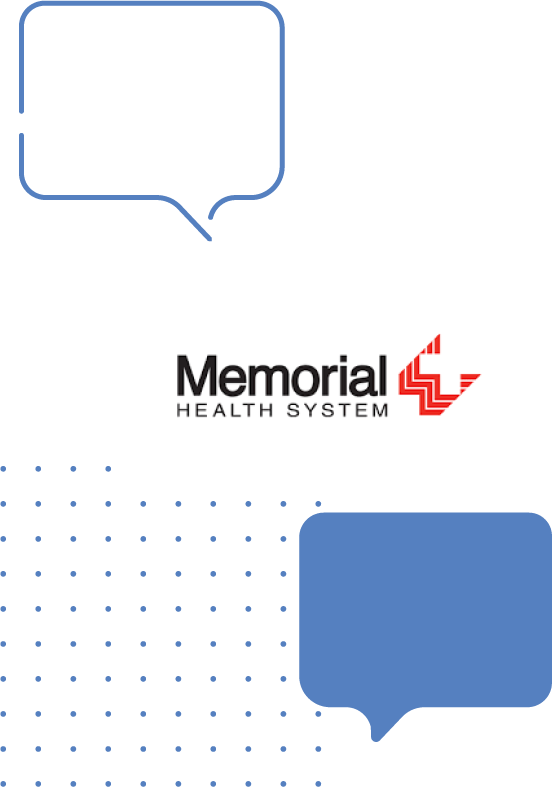
"Simul8 has been a valuable application for expanding our range and depth of analytical abilities. It should be considered an important tool in the design of every robust performance improvement program."
System Director of Operations Improvement, Memorial Health System
MHS ensures the feasibility of a $30m operating room expansion using Simul8.
Read the case studyFind out how these organizations used Simul8 to improve efficiency and increase profitability
Learn more about Simul8
Explore the wealth of features that make Simul8 the #1 choice for simulation.
Learn more