Establish balanced line, optimize throughput
Simul8 can help manufacturers to test and implement a well-balanced line that has the flexibility to hit targeted throughput consistently.
What is line balancing?
Line balancing is the leveling of the workload across all operations in a manufacturing line to remove any bottlenecks and excess capacity.
The 'line' could be an assembly line or modular line and will likely have many work stations with varied tasks and work contents.
Manufacturing throughput is dependent on the length of time each task takes on the line, the number of staff available and their skill level, machine capacity and in the case of mixed assembly lines, changeover times.
When designing and managing a mixed-model line assembly, system engineers strive to satisfy a number of objectives including:
- Maximizing line throughput
- Minimizing the number of stations
- Maintaining a balance of work across stations
- Satisfying delivery rates
- Accommodating product mix changes
These goals ensure that production schedules are continually met, manufacturing costs are kept low and ensure that the quality of goods is maintained.
What are the common challenges?
With so many different and potentially conflicting requirements on the system, as well as interdependencies between process constraints and design objectives, the outcomes of line balancing process design, or re-design, can be difficult to predict. If new processes create bottlenecks at any point in the system, this can negatively impact the whole line and overall throughput.
Designing a new system or re-designing an existing assembly line incorrectly can result in lost production, substantial revenue losses and overworked operators.
Analytical methods can be used, but are limited due to the dynamic nature of the system. The impact of buffering, shift patterns, and product sequence quickly confounds this approach for line design and balancing.
Other factors that add complexity to the design of an assembly line include:
- Reliability of equipment
- Availability of operators
- Size of line buffers
- Sequence and mix of product
- Delivery rates and volume
How can simulation be used to implement line balancing techniques?
Simulation can help manufacturers to quickly identify bottlenecks, test production schedules and evaluate the impact of design decisions.
With simulation, manufacturers can test changes and optimize a wide range of factors including shared resources, simultaneous tasks, mix product variants, downtime, over-cycles and changeovers.
Implement a balanced line
Simulation can help manufacturers to test and implement a well-balanced line that has the flexibility to hit targeted throughput consistently.
Gain confidence through insight
The insight provided through simulation gives developers, line managers, and stakeholders confidence that changes being made will have the desired outcome.
Evaluate production efficiency
Using line balancing simulation, manufacturers can identify system bottlenecks, test production schedules, and evaluate the impact of design and scheduling decisions, such as buffering requirements and product mix.
Perform thorough analysis
Manufacturers around the globe consider simulation essential for performing any rigorous and meaningful analysis on a modern production line, as it is capable of including the required level of detail and establishing confidence levels around results for a wide range of issues.
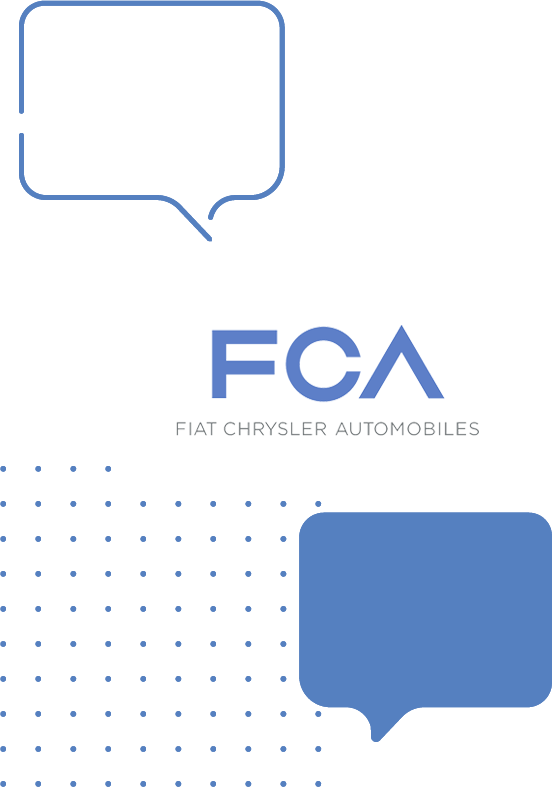
"Simul8 is fast and easy to learn. It’s quick to use which makes it an ideal tool for getting the results we need to make fast but thorough decisions."
Throughput and Simulation Specialist, Chrysler
Chrysler increases revenue by $1,000,000 per day without increasing costs.
Read the case studyFind out how these organizations used Simul8 to balance production flow and increase throughput
Learn more about Simul8
Explore the wealth of features that make Simul8 the #1 choice for simulation.
Learn more