HP achieves productivity gains, saving $100,000 annually
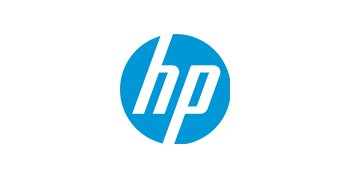
- Industry
- Manufacturing
- Location
- Palo Alto, California, U.S.
- Project goals
- Improve production throughput, process times and increase profits
Achievements with Simul8
-
-
Saved an estimated $100,000 annually
-
-
Identified other quick-win productivity gains
About the project
Hewlett Packard (HP) is a worldwide leader in the development and manufacturing of electronic equipment. For more than a decade, HP have been using simulation to improve production throughput, process times and increase profits to their bottom line.
HP used Simul8 to model the assembly and test process in the manufacturing of test and measurement products. The inputs for the simulation for one particular product family included a comprehensive mix of data, including cycle times for process stages, machinery failure rates, labor availability, shift patterns and storage capacities.
By varying orders and labor availability, HP's simulation could determine the most effective set-up of the production line. According to Ian Harrison, QMD at HP, the simulation not only met its objectives but also illustrated the delays and constraints within the process, and presented opportunities to reduce and eliminate non-value adding activities.
"Simulation is particularly speedy at highlighting the major constraints within critical processes and thus enabling the model builder to construct the correct event sequence and buffer sizes to keep the major constraints fully utilized."
QMD, HP
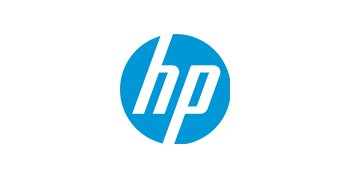
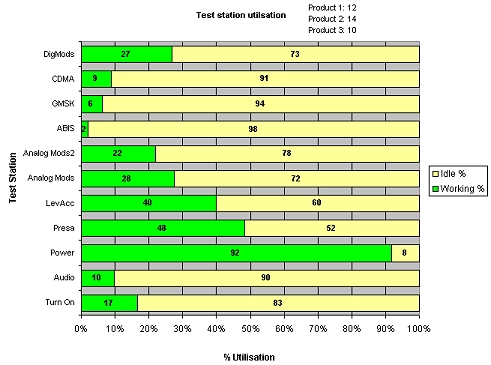
Expanding the use of simulation within HP
Within QMD Process Engineering, the number of simulation users quadrupled in a 12-month period. This is almost completely due to Simul8's comprehensive, intuitive and easy to use features.
Ian noticed "By dispersing simulation into the rest of the engineering community and first level management, many more processes are analyzed and improved". More users has also provided more opportunities for training and more innovative applications, as users continue to push the boundaries of simulation's use.
Another major benefit brought by Simul8 was that it provided a platform where simulation has become more familiar, and easier to use as a desktop productivity tool. As a training tool, it has become easier to illustrate management fundamentals such as Goldratt's theory of constraints or the need for Kanban.
This particular project saved HP an estimated $100,000 annually in opportunity costs as well as other productivity gains.
Learn more about Simul8 for manufacturing process improvement
Find out more about how simulation is used by manufacturing organizations, read more case studies and access a range of learning resources.
Learn more