Plexus rapidly implements manufacturing process improvements
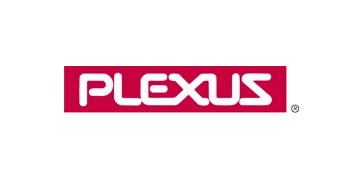
- Industry
- Manufacturing
- Location
- Neenah, WI, U.S.
- Project goals
- Identify manufacturing efficiency improvements
Achievements with Simul8
-
-
A 95% production confidence interval on the volume of units which could be assembled for their client
-
-
Identified staffing levels required to meet this client commitment and customer demand
-
-
$5,000 in equipment savings that would have been purchased without simulation insight
About the project
Plexus is the industry leader in servicing mid-to-low volume, higher complexity customer programs characterized by unique flexibility, technology, quality and regulatory requirements. Award-winning customer service is provided to over 140 branded product companies in the Communications, Healthcare/Life Sciences, Industrial/Commercial and Defense/Security/Aerospace market sectors.
Continually looking at ways to utilize innovative technology in the solutions they provide to clients, Plexus recently utilized Simul8's discrete event simulation software to identify manufacturing process improvements at their facility in Wisconsin, where they assemble a revolutionary drink dispenser for a major global beverage client.
"I would recommend Simul8 because it is quick to learn and powerful to use.
It can save you from making costly assumptions in commitments to customers, as well as reducing the risk of buying new equipment without knowing the outcome of that purchase."
Industrial Engineer, Plexus Corp.
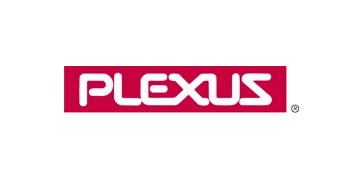
Fast, insightful manufacturing simulation results
Over the last 30 years, the manufacturing industry worldwide has become increasingly driven to be more effective and reduce operating costs. Many manufacturers, including Plexus, are utilizing Simul8's discrete event simulation software to continually improve their processes and achieve lean, sustainable supply chains.
Ben Van Straten, an Industrial Engineer at Plexus' Appleton facility recently utilized Simul8 to develop a simulation model of their current Aftermarket Service department (AMS) in order to assess and optimize production capacity for an innovative beverage dispenser.
This AMS department remanufactures returned dispensers, as well as field replacement units (FRUs) which are parts and components which are sent out to be replaced.
The manufacturing line follows the dispensers around the facility, as well as the sub-lines that both acquire items externally and from the dispensers themselves, to then either be sent back out or put back in a dispenser.
Within the department there are also multiple shifts, machine and location constraints, as well as travel time across the building.
After hands-on training with Simul8, Ben and an industrial engineering intern were able to rapidly develop an initial simulation within days; mapping the facility's various processes, resources, constraints and historical manufacturing data in the simulation.
Ben's assumptions were also validated by factory managers, supervisors and operators to ensure the simulation was reflective of real world conditions and included any nuances in the manufacturing process.
"The project began on a Friday and was able to be completed in its rough draft by Tuesday of the next week.
The simulation was then tweaked a few more times over the course of that same week to answer specific scenarios about how the manufacturing area could be optimized, how production capacity could be expanded, and what gaps we had currently versus what the simulation results showed that we needed."
Why was Simul8 chosen as the best simulation software solution for Plexus?
"We chose Simul8's simulation software for Plexus as it was cost effective, required minimal coding background, and gave us extraordinary power with simple setup.
The development and sales teams at Simul8 were also very helpful and provided a wealth of simulation and process improvement knowledge both before and after coming on-site to train us.
In terms of using Simul8 versus value stream maps or other lean tools, the major advantage of simulation modeling is the fact that they can be easily updated, changed or added to at any time.
Simulation enables us to create multiple scenarios where we can test our assumptions, validate variances between processes, and see how our distributions affect our manufacturing line. It also allows us to blatantly see any issues in the process versus having to find them."Ben Van Straten
Industrial Engineer, Plexus Corp.
A powerful tool for manufacturing decision making
Plexus' results with discrete event simulation provided valuable insight in just a few days and enabled several key manufacturing decisions to be made:
- The simulation results enabled Plexus to provide their client with a 95% confidence interval on the number of units that could be assembled based on current infrastructure constraints.
- As well as showing how many units could realistically be produced, the simulation also provided Ben and his team with valuable recommendations for the optimum level of staffing that would be required to meet this manufacturing commitment.
- Simul8 also quickly saved Plexus over $5,000 by proving that the purchase of additional machinery to add capacity to parts of the assembly process was not necessary.
With the ability to run different production scenarios within the simulation model, Plexus could also quickly identify areas where production output could be increased if required, and importantly, what the impact of this would be on manufacturing KPIs and costs.
The simulation of the manufacturing floor has been so successful that it is now utilized as a live document which is updated on a weekly to monthly basis for ongoing production capacity information and process improvements.
Building on Plexus' simulation success
"After only a few days of training, I feel confident that I can make multiple, diverse manufacturing simulation models that can help Plexus continue to challenge its practices and make strong, informed decisions about how to move forward."
"More recently, we have started to map our forklift process of receipting in parts to understand if we are truly utilizing them enough to keep rental equipment in-house or send them back. It will also very quickly show us what our staffing levels need to be in order to support our manufacturing area as our customer base grows."Ben Van Straten
Industrial Engineer, Plexus Corp.
Learn more about Simul8 for manufacturing process improvement
Find out more about how simulation is used by manufacturing organizations, read more case studies and access a range of learning resources.
Learn more