Simul8's five steps to simulation project success
Check out our tips for structuring simulation projects to engage stakeholders and meeting the goal of making faster, confident decisions.
Setting your simulation project up for success
Simulation is a powerful approach for getting evidence to plan and improve processes in a risk-free environment, ahead of implementation. But because it’s so powerful, it’s often easy to focus on the quantitative power rather than how it can be used as part of a transformational change process.
Engaging stakeholders in decision-making, drawing on their insights to understand how the current system operates, and encouraging their views on how to make improvements, are all just as important for the success of any simulation project.
So how can you structure your simulation project in a way that helps captures this valuable insight? Here are our five recommended steps for structuring simulation projects to engage stakeholders and meet the goal of making stronger, evidence-based decisions.
-
Step 1: Agree the initial question and the results you’ll need
People will often come to you at the start of a simulation project with high level problems – for example, “we want to reduce costs” or “we need to improve throughput”.
As the facilitator, the simulation expert should ask questions to help the problem owner pinpoint the part of the process they need to focus on. This will enable you to define the key question the simulation should answer and agree the results that will be needed to help make decisions to solve the initial problem.
“It is very important that we define our project scope up front. Anybody who has been involved in project management knows the pitfalls of scope creep! It’s not a bad thing if we want to start asking different questions, but we need to be clear about the key question up front, and that our project is really focused on that. As we discover different things, then we can increase learning through further projects, or perhaps increase the project scope in a methodical way.”
Eric Hamrock, Innovation and Continuous Improvement Facilitator at Howard County General Hospital
-
Step 2: Build a preliminary simulation and test it with stakeholders
Once the key question has been agreed, start sketching out the simulation process flow with the stakeholders who are involved in the process day-to-day. Look at easy to access data for key points of the simulation, for example, patient numbers in a hospital or call volumes in a call center.
The simulation can then be tested to produce results at key points to validate against real data of the current state – this might be throughput rates, overall time in system, etc.
As this is the simulation you’ll use to engage stakeholders, it’s valuable to gain their insight into the process, understand the challenges they face, and the solutions they would like to try to overcome the problem.
You might also find it helpful to run a workshop session with these stakeholders that will allow you to:
- Agree that the process is right
- Capture any feedback or refinements
- Agree results they need to see
- Define the “what if?” change scenarios to be tested
- Identify who can help with any data questions
“We start out with a simplistic simulation model, something that is not as time-intensive to put together. This allows us to get management understanding how simulation works and the kind of data we’ll need. We do an initial phase to prove out the concept and get some feedback and then we go in at a much detailed level.”
Seth Hostetler, Lead Process Engineer at Geisinger Health System
-
Step 3: Refine the simulation and test improvement scenarios
It might be necessary to run a few of these workshop sessions to make any refinements, revalidate, and identify the learning that stakeholders are getting from the process.
As a result, you might actually find that the initial assumptions and question will evolve at this point: “We started this project thinking that equipment was causing bottlenecks, but it turns out that it’s staffing scheduling issue”.
The simulation is already providing value – allowing stakeholders from different parts of the process to evaluate the problem from every angle. The results from the simulation can then be used as evidence to develop better, more relevant questions before making decisions.
At this stage, you can compare the current state with the outcome of the simulation scenario results to help stakeholders understand which improvement strategy will be most effective.
“Our project began on a Friday and the simulation was able to be completed in its rough draft by Tuesday of the next week. We then tweaked the simulation over the course of that same week to answer specific scenarios about how the manufacturing area could be optimized, how production capacity could be expanded, and what gaps we had currently versus what the simulation results showed that we needed.”
Ben Van Straten, Industrial Engineer at Plexus Corp.
-
Step 4: Detail the results and share the simulation in a final stakeholder workshop
Once all the simulation iterations have been completed, take the final simulation and its results to a decision-maker workshop.
This is where you outline the process and compare the current state with the best improvement results, enabling decision-makers to reach a final recommend solution from the evidence provided by the simulation.
Tip: With Simul8, you can easily share your simulations with anyone. Shared simulations can be opened in a browser, allowing anyone to run and experiment - no downloads or installation needed!
“This is where we’re providing the information to the management team. We’re not making the decisions for them, but we are able to provide them all the necessary information to help answer the questions they need to make those decisions.”
Seth Hostetler, Lead Process Engineer, Geisinger Health System
-
Step 5: Implementing the findings
When approval has been given, you will likely need to document the simulation, inputs, outputs and data sources and any analysis for the final business case. It’s often easier to document these as the project progresses as it will make it much quicker to pull this information together.
For some of our users, the simulation work stops at this stage with mission completed, but others might continue to use the simulation with refreshed data to monitor implementation and pinpoint other parts of the process that could also be improved.
“The insight provided through using simulation enabled us to make a strategic, long-term capital plan, as well as product offering decisions. The project has been quickly approved and the design and engineering work is already in process, with the goal of implementation later this year.”
Eric Kurtz, Project Manager at FUJIFILM Imaging Colorants
More examples of Simul8 users who have transformed decision-making with simulation
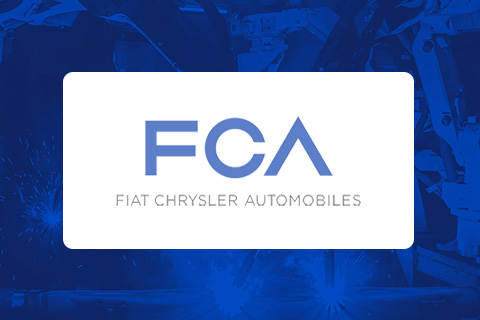
Meeting increased demand without additional costs
Fiat Chrysler improved manufacturing throughput by 39 units and increased revenue by $1,000,000 per day at its Brampton plant.
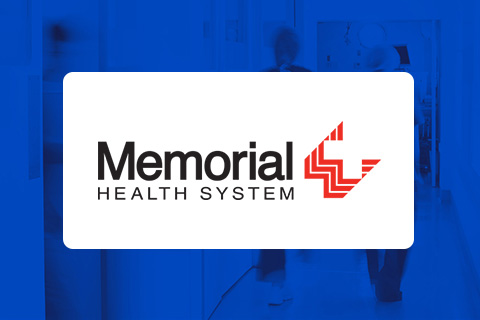
Ensuring the feasibility of investment and expansion
Memorial Health System improved patient waiting times and ensured the feasibility of a $31 million capital investment project.
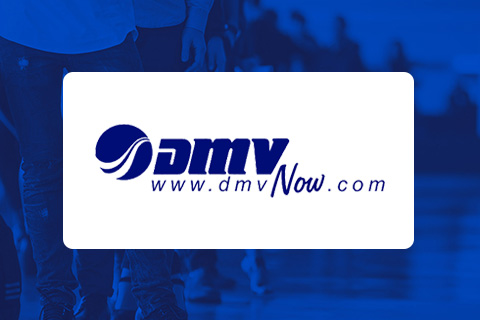
Optimizing staffing to reduce customer wait times
Virginia DMV identified a staffing model to reduce customer waiting times to 20 minutes or less across 74 customer service centres.
Learn more about Simul8
Explore the wealth of features that make Simul8 the #1 choice for simulation.
Learn more